Editors note: This is a guest post by Ethan Hagan from One Project Closer.
A Quick Intro
Maybe you don’t think a workbench is really all that important. After all, you’ve only got a few tools and everyone knows the folding table in the basement is your space. A dedicated workbench isn’t worthwhile, is it? I’ve seen too many guys stashing their tools in a kitchen drawer or expecting their kids to not touch the freshly painted picture frame. You need a proper place to work and store your tools, and I’m going to show you how to build it.
How to Build an All-Purpose Workbench
Your workbench is going to have some key features like a strong, rigid work surface, power for your corded tools or chargers, a shelf to store tools and accessories, and wheels so that you can move about. The materials are going to run about $120 (cheap ≠quality) and you should secure a drill/driver, miter* saw or circular saw*, and jig saw* before getting started. (*You can substitute a handsaw if you’re up to the challenge.)
Materials:
Head over to the local home improvement center with this shopping list:
- (1) sheet of 3/4″ sanded plywood
- (1) sheet of 3/8″ plywood
- (9) 2—4×8’s
- (8) Simpson rigid tie connectors (see below)
- (200 count) #8 x 1-1/4″ screws
- (4 count) 3″ screws
- (1) tube of heavy-duty construction adhesive
- (4) 2-1/2″ locking casters
- Mountable power strip
I’ve listed nominal plywood thicknesses, however the store will display actual thicknesses. For instance 3/4″ plywood is actually 23/32″ and 3/8″ plywood is actually 11/32″ thick. Sanded plywood will give you a nice, splinter-free surface, and, at 3/4″ thick, it’ll absorb a lot of deflection.
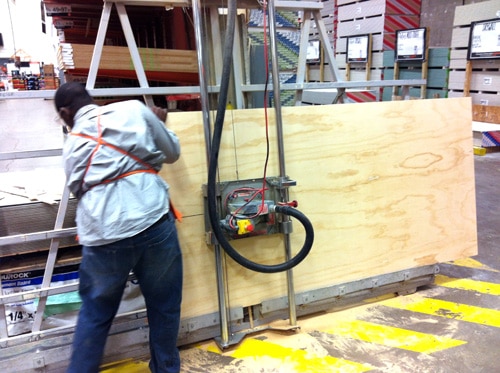
Have the store rip both sheets of plywood in half (resulting in 2 x 8′ pieces) to save some work.
Straight boards make for a straight workbench, so look down the length for any cupping (side-to-side curve) or crowning (up-down curve), and put those boards back.
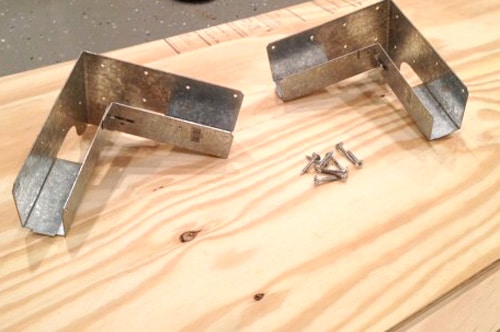
The Simpson ties are awesome because they form the corners of your workbench and shelf. Without these, you’d need a lot of angled braces.
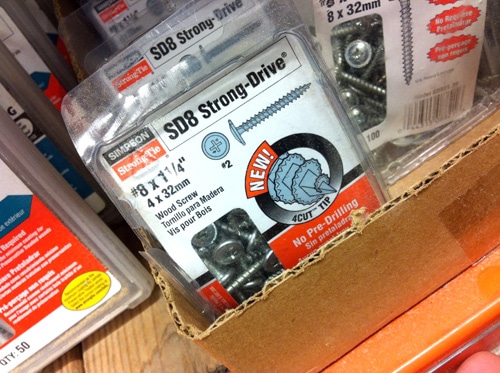
The #8 screws are usually sold right next to the Simpson ties because they’re designed for each other.
Down to Size
Since the home improvement center ripped the plywood for you, all you need to do is cut the 2×4’s down to size. Use a square to mark straight lines. Here are the lengths:
- (5) 90″ for the lengthwise supports
- (4) 17″ for the width-wise supports
- (4) 36″ for the legs
- (2) 24″ for the caster supports
Let me save you some confusion and tell you that the plywood is going to overhang one side by 3″. This is on purpose because that overhang will protect the power strip that we’ll mount to the side.
Some Assembly Required
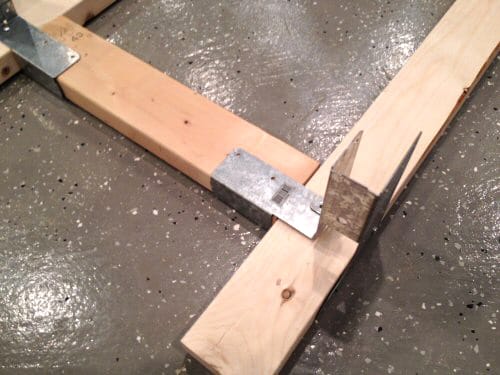
To put this beast together, start with the sides. Grab a leg and width-wise support and slip a Simpson tie in place. Use pieces of scrap to make sure all the heights line up, and be sure to orient the legs the same way we show in the pictures.
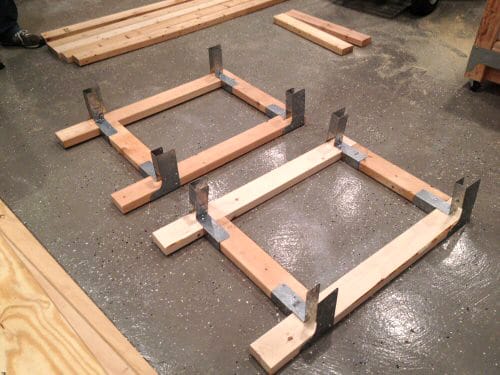
Remember, you need two Simpson ties per leg (one for the work surface and one for the shelf), and corresponding ties should sit at the same height. Put screws in all of the pre-drilled holes, keeping each piece firmly against the adjacent pieces.
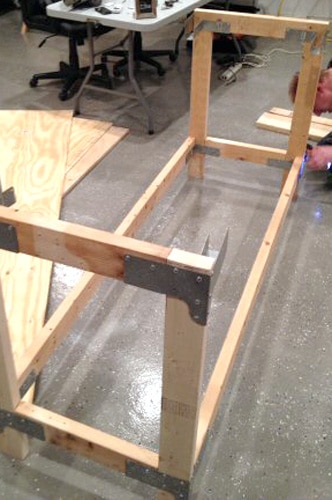
Now it’s time for the length-wise supports. There are five of these because we’ll use the extra to reinforce the work surface.
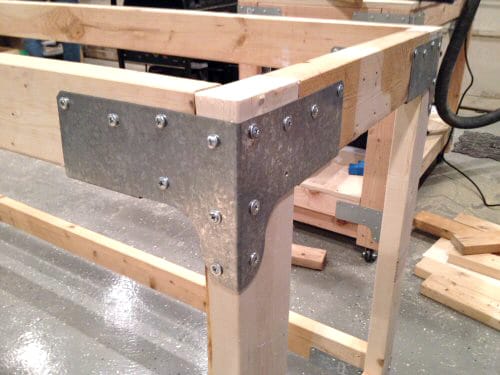
Run the extra support centered between the other two, and secure it through each end with two 3″ screws.
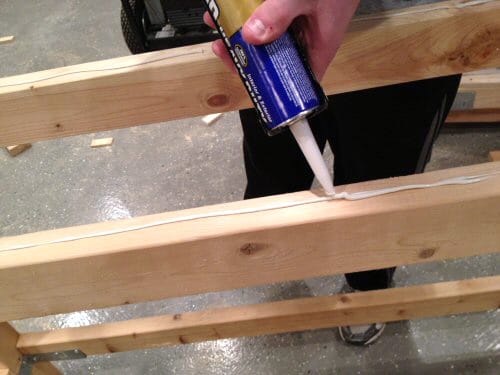
Before you put on the 3/4″ plywood top, run a bead of construction adhesive on all the supports. Put screws every 16″ or so. Once you’re finished, flip the table upside-down.
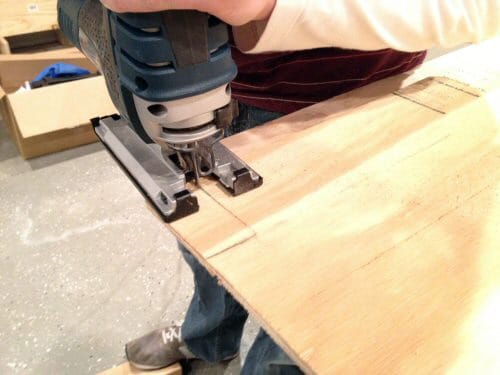
Next, grab one of your 3/8″ plywood pieces and cut 2×4 notches in all the corners to account for the table legs. I used a jigsaw but a handsaw would work just fine. Do the same for the remaining piece of 3/4″ plywood.
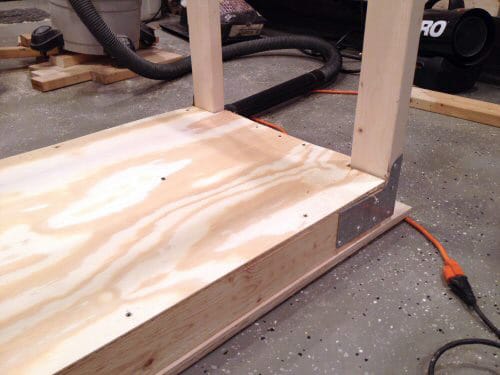
This piece of plywood is going to be fastened to the underside of your work surface. It may seem odd, but this “torsion box” design will further improve the rigidity of your work surface. Glue and screw just like with the 3/4″ plywood.
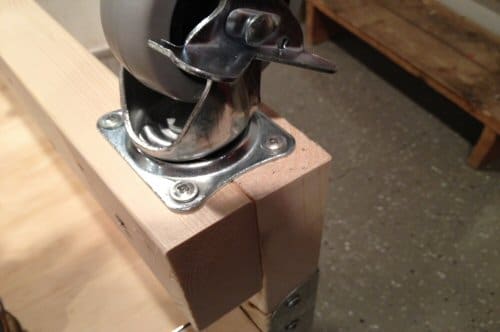
While it’s upside-down, screw those caster supports between the table legs and then fasten the casters in place. These supports are important because otherwise the caster is only sitting on end-grain which makes for a weak joint.
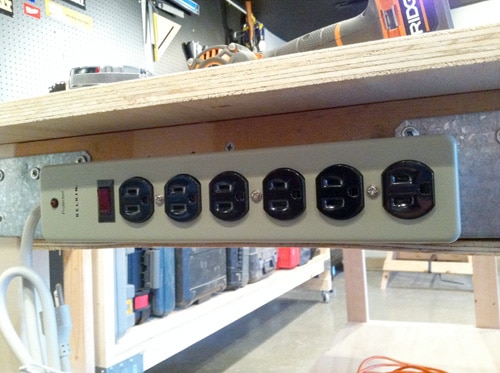
Flip the bench right-side-up and put on the 3/4″ plywood (glue and screw) for the shelf. Lastly, mount that power strip underneath the overhang. This’ll help prevent sawdust, paint, oil, etc. from damaging the strip.
Gloat
Step back and marvel at your creation because you have just finished building a hardcore workbench. Go ahead and feel the solid work surface that won’t bounce when you’re hammering something together. Unlock the casters and move your workbench around the room. Set up a battery charger on the conveniently mounted power strip. Best of all, call up your friends and brag.
_____________________________________
Ethan Hagan is the primary editor at One Project Closer. He spends most of his days shadowing real contractors on actual job sites and most of his nights writing about the experience. To see what I mean, check out their latest “Pro-Follows” or finished, expert guides on things like How to Build A Shed and How to Build a Deck. If learning and interacting with pro contractors sounds like something you’d enjoy, sign up for OPC email updates.