“An object should be judged by whether it has a form consistent with its use.†– Architect Bruno Munari
In her book The Not So Big House, architect Sarah Susanka postulates that we tend not to build living structures that reflect how we actually live. Homes are sometimes built to impress the people outside rather than be comfortable for those inside. Vaulted ceilings and master suites are regal, but go to a party and see where people hang out: in the kitchen or smaller rooms.
Susanka stresses creating spaces that suit what you really do. A formal dining room may seem elegant, but unless you’re throwing dinner parties on a regular basis, it’s a waste of space. Most of my friends who live in homes with formal dining rooms end up turning them into home offices or game rooms.
We moved to a new (to us) place about 12 years ago, which more than doubled our living space. Going from an 800 square-foot two-bedroom home to one with over 2000, we were stunned. My wife and I were forced to look at things differently. We gave serious thought and reflected on how our family lives, and came up with a plan that utilizes space in a way that most reflects our values.
This is also manifested in our former garage, which hasn’t had a car in it in 11 years. That’s because my garage is a blacksmith and woodworking shop on one side, and canoe, kayak, and bike storage on the other side.
Now I understand the allure of putting cars in a garage. If I were lucky enough to have a 4-car garage I would definitely put our cars to bed under a roof, but city life means compromises. Which to give up? Obviously we made the right decision…for our family.
If you’ve ever thought about turning your garage into a blacksmithing or woodworking shop (or both), below I offer some thoughts on how to do it, as well as why you should consider making your dream a reality.
What if I want to transform my garage (or part of it) to a shop?
If you’ve read this far and think I’m not half a bubble off plumb, let’s assume that you desire to perform such a transformation. Here’s what I did.
First, marry well.
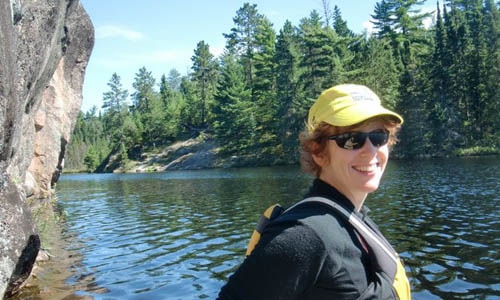
The one who made all this possible.
I’m only half joking here. Some partners would not give up their parking space willingly, if at all. My conversation went something like this:
Me: “Honey, can I talk to you about the garage? I’m considering…â€
Wife: “So what sort of shop do you want to build on my side of the garage?â€
Me: “A blacksmith shop.â€
Wife: “Thought so. Well, I expected that. Sure. My car is waterproof. Go ahead. Just don’t burn the garage down.â€
Me: [weeps with gratitude]
Second, start sketching out a floor plan.
You don’t need to be a draftsman to lay things out. Graph paper is plenty sufficient. Think about the scale of things you might build. A friend of mine built a kayak and later found he had to saw it in half to get it out of his basement shop (don’t worry, he put it back together again). In my case, my work area is fairly compact, and the line between the woodworking area and the metalworking area is somewhat blurred.
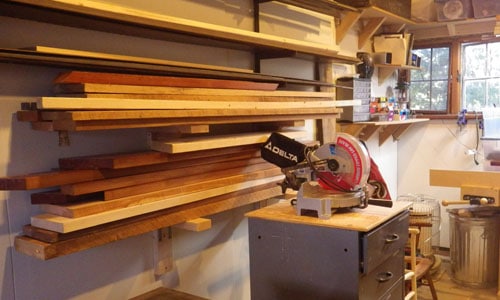
I can’t resist a piece of 5/4″ hardwood.
For blacksmithing, laying out the workspace is critical, since your medium has a working time. It’s sorta like a dance between forge, anvil, and vise. You stand in the middle of the triangle. No wasted steps.
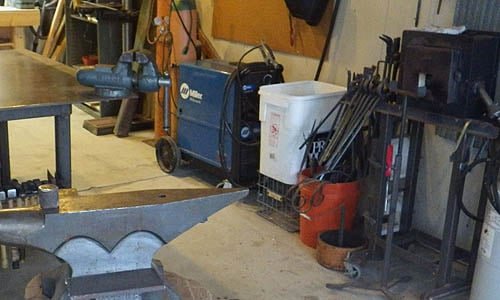
The triangle.
Also pay attention to power. If you have a welder of any size you’ll need to run more power to the workspace. I have 100 amps just going to the shop (the house gets the other 100). The welder takes 50 amps at 220 volts. Then again, I bought bigger than I needed, but you never know when you might need to weld 1″ steel plate.
I have several outlets for the welder, one near the garage door so I can wheel the whole welder to the driveway if necessary.
Third, acquire tools…slowly.
It’s tempting (if you have the cash or a big limit on your credit card) to rush out immediately and load up on all the coolest and latest. This is a mistake for a few reasons. First, you’d probably buy tools you wouldn’t need, at least for a while. It’s a common disease that occurs in people setting up a shop: the Shiny Tool Syndrome. This is especially bad when tools are packaged together. Which leads me to the second reason: you’d buy crappy tools.
A far better approach is to purchase tools as you find you need them, and buy good tools from reputable resources. Big box stores have good tools, but you have to look, and you have to be willing to pay more. Most of the big boxes have large sets of tools, usually packaged together. Check the label: American Eagle Tool Company might sound good but chances are they’re made in China.
Blacksmithing tools are not sold at the local box store. They are highly specialized and to buy cheap ones is to really handicap yourself from the start. There are a few really good supply houses like Centaur Forge and Kayne and Son.
For woodworking, tools are a little more straightforward. What do you need to start? That all depends. Like blacksmithing, you need tools to shape the wood. If you’re doing a lot of woodcarving, good chisels, gouges, and files are more important than planes or drills. Making cabinets? You’ll need planes, chisels, and a lot of clamps. N.B.: you cannot have too many clamps. See the fourth point below, it’ll help.
Once you know what brands are reputable, you’ll have a lot more purchasing power if you visit antique shops and attend swap meets and barn and garage sales. You might get lucky and score a nice plane for $25 that cost $200 new. I’ve found good hammers and tongs, as well as some clamps and vises this way. I once bought an entire coffee can (the smaller kind) of metal chisels and punches for $15.00 out in the middle of the desert somewhere.
The quality of the metal in older tools is superb, and steel wool, gun oil, and some elbow grease can really bring them back to full function. Naval jelly, a rust remover, can work well too, but rinse and treat soon after using it. Learn how to recondition tools and you’ll save a bunch of money.
I would, however, shy away from buying an anvil at a barn sale or swap meet. It is one of your primary tools (hammers being the other), and if it’s too far gone you’ll be frustrated.
You may not have to buy all the tools you need, either; a nice side effect of building your own shop is that people will bring you tools, sometimes for nothing. A good friend brought me a box of old tools that belonged to his Uncle Stanley. Some of the smaller tools with lots of moving parts were too far gone, but the late 1800s wood-body scrubbing plane needed only a little wood glue and a little sharpening…it scrubs wood off beautifully.
The box also included a dozen or more cold chisels and hot cutters for metal work — useless to most people, but a bonanza for me. After removing the rust and polishing them up a bit, the quality of the tools is amazing.
The cost for this box of treasures? Nothing. “I just wanted them to go to someone who would use them.†Well, that’s easy. Use them I will.
In short, spend more, buy less. Buy good stuff once instead of bad stuff twice. If you have to delay gratification, man up and wait.
Fourth, find a mentor.
Although they are getting scarce, there might be an old guy on your street who has a shop to die for. He knows how to recondition a plane, get rust off an old vise you bought at a garage sale. He also knows which brands are worth buying and which ones aren’t. My mentor taught me the value of a $45 Armstrong C-clamp over a $12.99 (or two for $19.99) Harbor Freight American Tool C-clamps.
A mentor can also critique your work and give you ideas on the subtleties of a particular technique. A book about dovetails is good; a mentor who has made dovetails is great.
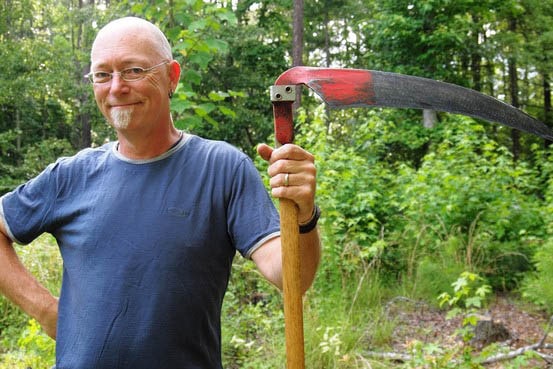
Larry Cooper, master blacksmith, welder, and scythe dude
Larry Cooper, my blacksmithing mentor, taught me a lot about metalwork, but he also taught me a lot about life. Being from Alabama, he was a might more laid back than I, and helped me learn to slow down and see things better. Not just when making a piece of art, but driving the backroads, eating a meal together, or just sitting and talking.
Why would you want to transform your garage into a shop?
A Shop Makes You Neighborly
Having a shop in my garage attracts attention, especially the blacksmith part. My anvil has a nice ring to it and people walk by and wave. If I stop hammering, people come to see what’s going on. Sufficeth to say when people need help, they come over. I refuse payment for little things.
I have sharpened countless lawnmower blades. I like doing that; it’s fast, easy, and generates more neighborly interaction. I’ve rolled the welder out into the driveway to tack down a broken metal bracket on a pick-up truck. A few years ago I fabricated a little aluminum arm to save a $400 stroller from the dump. Now that was neighborly.
You can also provide mentoring skills up to your level of competence. You don’t have to be a woodworking master to show a kid how to use a handsaw. Or for that matter, a friend your age who has never touched a handsaw. A lot of skills are being lost every day as time passes. You can provide a bulwark against this decline.
Men will want to gather around and hang out. I have a few folding chairs that hang on the wall of the shop. A small refrigerator ain’t a bad idea either. Just don’t drink and saw.
A Shop Makes You a Better Man
One of my favorite books of 2009 is Shop Class as Soulcraft by Matthew Crawford. Crawford has a PhD in Political Science from the University of Chicago. He’s no dummy. His book discusses the cultural implications of “knowledge workers” being more valued than those who do tangible things. He argues that this equation is wrong-headed and that there is indeed enormous value to manual labor — work which connects the hands and the mind.
Cultivating this connection is important for those in white collar professions who spend their days doing abstract work. Get some balance by turning to a hands-on hobby during your nights and weekends. Working with your hands teaches your brain to work better. It makes you more self-sufficient and more useful to the community. It makes you whole.
You don’t have to be a master woodworker or blacksmith to gain the benefits of having a shop. Indeed, quite frankly, I’m what I would call a skilled hack. I try things, and if it works, it works. My work isn’t going to show up in Fine Woodworking or its metal equivalent (there really isn’t one), but it makes me happy.
And it’s funny how a space like this gathers men. No cracker barrel or checkers set. Sometimes we bang on metal and sometimes we don’t. It doesn’t matter.
It’s also where I play the banjo because it doesn’t bug anyone but me.
Is there a downside?
Of course, there are negative effects of turning your garage into an alternative space: your car will get wet. Last I checked, however, our cars are waterproof. UV is a problem for paints and exteriors, but a car cover is cheap insurance, especially if you go a long time without driving.
You may find it’s easier to bring in dust and dirt, especially if your garage is attached to your home. If you end up doing a lot of woodworking, you’ll probably want to invest in a dust control system, but until then, use coveralls when you can, blow your clothes off with an air compressor, and leave the garage shoes where they belong.
Other than that, what’s keeping you?